WMEM | 数控机床防碰撞及碰撞保护技术研究与应用

【摘要】数控机床意外碰撞是造成机床长时间故障停机、精度丧失、关重部件减寿甚至损坏的一项重要原因,数控机床一旦发生碰撞,将给企业造成重大的经济损失,严重影响企业科研生产。目前普遍开展的是通过管理方式进行改善,规范操作及编程,降低犯错率。但如何从技术层面有效避免数控机床发生碰撞,或者即使发生碰撞,机床如何能快速停机,降低碰撞损失,实现碰撞保护,一直是摆在设备维护人员面前的难题,是设备维护人员研究和探索的技术方向。
数控机床尤其五轴数控机床,由于其机床本体结构、加工路径、操作、编程、工装夹具等极为复杂,一旦出现操作及编程疏忽,如刀具长度、工件原点设置错误,机床部件与毛坯件、工装、夹具等辅助部件发生运动干涉(见图1)等,都极易造成数控机床意外碰撞,轻则刀具破损,重则主轴、铣头、工件损坏,机床精度丧失,长时间故障停机等,给企业造成重大经济损失,严重影响企业科研生产。

图1 五轴铣头与工装发生干涉
目前企业主要从加强管理入手,规范操作及编程。如培训操作人员规范操作,要求加工前必须进行加工程序模拟仿真等,降低犯错率,从管理方面进行预防,取得了一定的效果,但机床碰撞事件仍时有发生。
如何从技术层面有效避免数控机床发生碰撞,或者即使发生碰撞,机床如何能快速停机,降低碰撞损失,实现碰撞保护,是值得设备维护人员探索的两个技术方向。本文将简要介绍和说明针对以上两个技术方向进行的研究与应用。
1. 数控机床防碰撞功能的研究与应用
随着数控系统不断发展和升级,数据运算处理能力不断增强。目前一些高端数控系统,已经陆续推出数控系统防碰撞功能,如海德汉数控系统DCM功能(动态碰撞监测功能)、西门子数控系统COLLISION AVOIDANCE功能(选项功能6FC5 800-0AS02-0YB0)、FIDIA数控系统VIMILL功能。该功能用于在数控系统中全面构建机床实际加工的数字化环境,实时监控机床部件、工装、刀具、夹具之间的空间位置,避免在机床运行过程中发生碰撞,提高机床运行安全性。以下就以海德汉数控系统DCM功能为例,进行介绍。
(1)DCM功能简介
海德汉DCM功能是通过海德汉Kinematics Design软件,应用几何形状,例如立方体、圆柱和平面,描述工作区和碰撞对象,同时还可以组合多个几何体构成复杂的机床部件,最后将这些3D实体插入到机床运动链中。
在机床实际加工过程中或测试模式下,DCM软件都能实时监控这些机床部件的相对位置,如果部件之间的间距小于3-5mm,则数控机床立即停止运动,同时数控系统会出现报警提示。DCM功能对数控系统要求:①#40选项功能“DCM Collision”;②MC 422B/C;
③系统版本不低于340 49x。
(2)DCM功能使用方法
一台德马吉五轴加工中心采用海德汉iTNC530数控系统,配有DCM系统功能,以下就以该设备为例,简单介绍该功能的使用方法。
①建立机床部件实体。首先需要搭建机床的主件3D虚拟模型,通过使用Kinematics Design软件对机床部件进行描述定义(见图2),通过使用限位面描述工作区域的限制,使用立方体以及圆柱体描述机床的一些主要部件,如工作台、主轴头、立柱、刀库等。
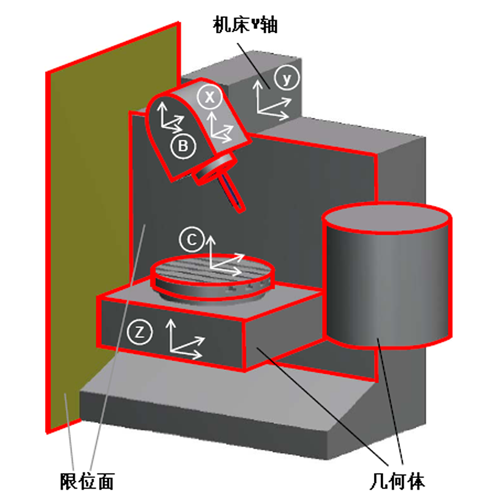
图2 机床主件模型
②建立夹具以及刀柄实体。同样是使用Kinematics Design软件对常用夹具以及刀柄进行描述定义,并将生成的模板文件拷贝到数控系统TNC分区的根目录下。为了生效夹具以及刀柄,必须在Kinematics Table中扩展定义TOOLFILE以及Clamp,如图3所示。
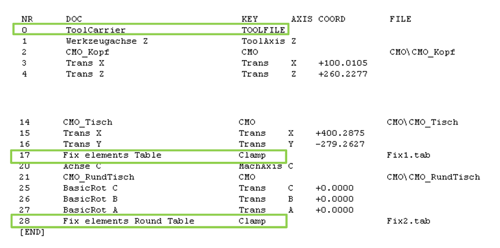
图3 Kinematics Table
③DCM功能使用方法。完成以上配置后,可在海德汉iTNC530数控系统上使用DCM功能。在手动操作菜单项中,进入COLLISION界面,可分别在程序运行和手动操作状态下打开或关闭DCM功能,如图4所示。
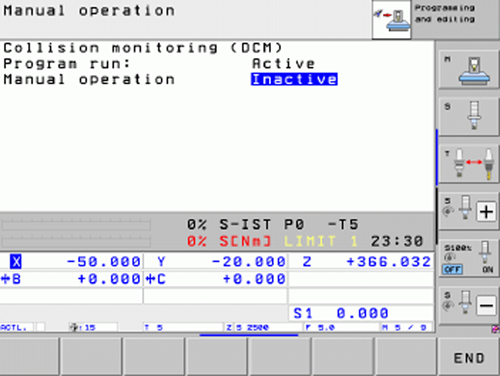
图4 激活DCM功能界面
由于机床厂家已经描述定义了DCM系统中的机床主体部件,为实现夹具监控,需要进入FIXTURE MANAGEMENT界面,如图5所示,调用夹具模板文件(后缀名.cft),并根据实际情况修改模板尺寸并保存(后缀名.cfx)。然后进入PLACE界面,利用机床配置的接触式探头测量功能,测出夹具在机床区域内实际位置。
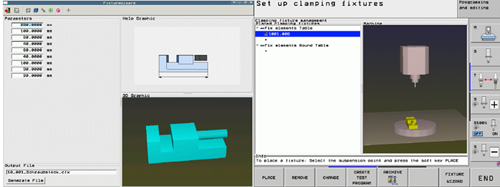
图5 夹具设置界面
关于刀具参数,如刀长、直径等,数控系统可以从刀具表中获得。但刀柄的形状则各不相同,为了实现刀柄监控,还必须对刀柄的形状进行描述定义,如图6所示,设定方法与夹具设置方法类似。
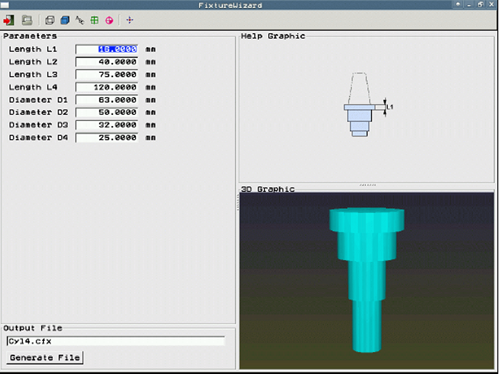
图6 刀柄设置界面
在完成以上步骤后,一个模拟机床的实际加工环境建立起来了。当机床移动时,DCM功能实时模拟运行,当监测到刀具与夹具之间距离<5mm时,存在碰撞风险,数控系统会立即停止加工,并弹出报警提示信息DCM:Tool-Flex Jaw,如图7所示。
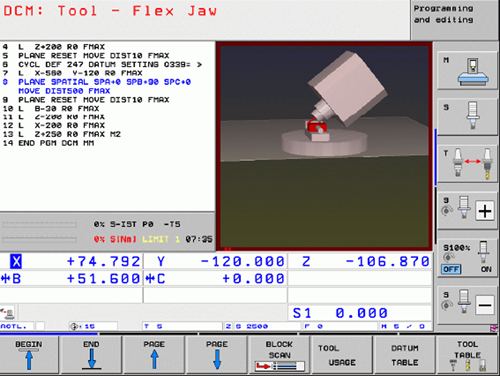
图7 DCM报警界面
2. 数控机床碰撞保护功能的研究与应用
研究表明,大部分伤害不是由碰撞本身造成的,而是由碰撞发生后瞬间持续的压力状态引起的,从碰撞发生到停止之间间隔的时间越长,则损害越大(见图8)。数控机床发生碰撞后,数控系统会增加进给力以达到设定的目标坐标点,直到伺服电机扭矩或电流监测超过数控系统设置的限定值,且达到一定的持续时间(以西门子数控系统为例,持续时间200ms)后发出停机指令,并弹出报警提示信息,在此期间,机床与工件开始损坏、精度开始丧失。如何最大限度降低机床碰撞造成的损失,需要快速判断机床是否发生碰撞,一旦判断为碰撞事件,数控机床快速反应停机,才能将损害降到最低。

图8 碰撞损坏状态
(1)碰撞保护功能
以一台三轴立式加工中心为例,在机床主轴端安装振动传感器,如图9所示,越接近主轴鼻端效果越佳。通过振动传感器进行数控机床碰撞识别,通常振动加速度≥30m/s²时,判断为碰撞事件,同时监控模块在3ms内发出报警信号,给机床控制系统触发急停报警,机床快速停止,如图10所示,将碰撞造成的损坏降到最低。
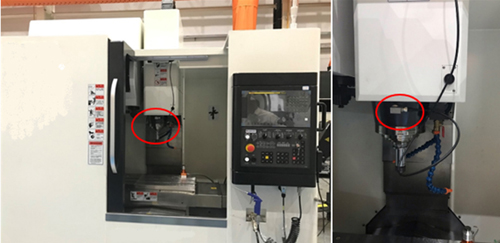
图9 传感器安装
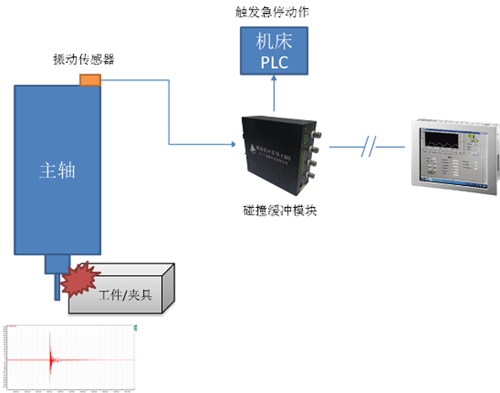
图10 碰撞保护原理
(2)碰撞保护功能测试试验
①试验条件:一台三轴立式加工中心,配置FANUC 0I数控系统,以G00速度(最大移动速度)分别从X和Z方向进行两次撞机测试(具体条件如表1所示),测量撞机前后主轴静态和动态精度差异,用以验证碰撞保护功能效果。
表1 测试条件

撞机前后主轴精度测量方法主要有动态精度和静态精度法。
静态精度法:使用千分表测量在0mm(近端)和300mm(远端)处的跳动,以及主轴轴线与Z轴在Y-Z平面和 X-Z 平面的平行度,如图11所示。
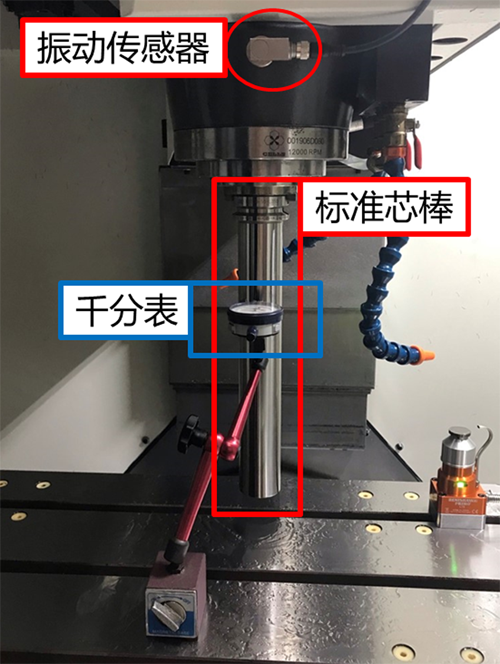
图11 主轴精度测量
动态精度法:利用三向振动传感器,测量主轴4000r/min空转时,在X、Y、Z三个方向主轴振动值,评估主轴轴承状态。
②试验结果:通过两次撞机测试,检测撞机前后主轴静态精度和动态精度(如表2、表3所示),主轴静态和动态精度均未发生明显变化,碰撞保护功能效果良好。
表2 主轴静态精度
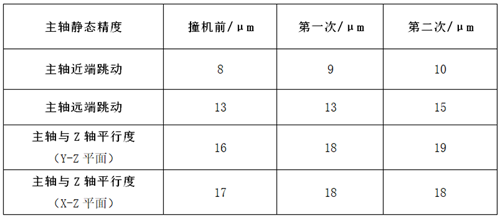
表3 主轴动态精度
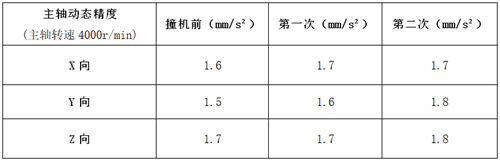
3. 结语
数控系统的防碰撞功能,对于数控系统硬件配置以及系统版本都有较高的要求,同时需要搭建数控机床实际加工的数字化环境,因此不但需要数控机床本身的数模,且对于常用的刀具、夹具以及工装都需要建数模,以致该功能的使用难度较大且过程较为繁琐,但实现后能够有效预防和避免碰撞的发生。
而采用振动传感器监测的数控机床碰撞保护功能,对数控系统本身配置没有要求,安装调试完成后就可以直接使用,功能实现较为简易,但是需要额外的硬件采购成本。此外,该功能实现的是碰撞保护,无法预防碰撞的发生,只能降低数控机床碰撞造成的损失。
因此可根据数控机床的实际配置情况,灵活选用这两种功能,对于新设备,在采购阶段要求机床厂家配置数控系统防碰撞功能,而对于老旧设备,数控系统配置无法满足防碰撞功能需求,升级换代的经济成本太高,则可考虑采用碰撞保护功能。通过采用这两种方式,可以从技术层面有效解决数控机床碰撞问题。
作者:胡辉 洪忠杰【昌河飞机工业(集团)有限责任公司】
来源:《世界制造技术与装备市场(WMEM)》杂志2022年第2期