在竞争日益激烈的市场环境下,准时化生产(Just
In
Time,JIT)的理念已为国内外众多企业普遍接受和倡导。然而,传统的JIT方式是从丰田汽车公司规模生产的实践中总结出来的,其理想的生产环境是大批量、重复性生产,与目前多品种、小批量的市场环境大不相同,直接套用显然不适宜,也不可能取得成功。
要使先进的管理理念成功运用于新的市场环境,必须进行“创新的应用”。将看板技术与信息系统相结合,是目前国内研究和应用的新热点,国外研究者也对JIT生产方式中的看板技术进行了大量研究;丰田生产方式不适合于多品种小批量生产。但在这些文献研究中鲜有对多品种、小批量看板方式的深入研究。
本文提出了一种基于可视化看板(www.hzjux.com)技术的解决方案,用于解决JIT方式在多品种、小批量生产中的适用性问题。
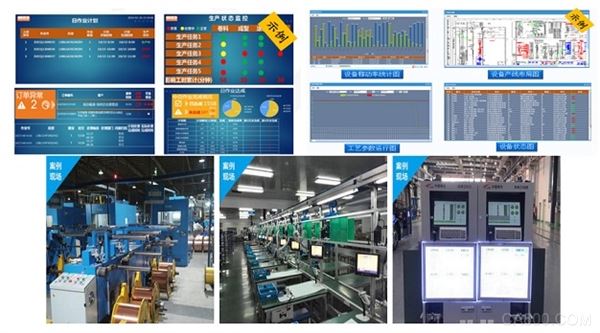
1、传统看板用于多品种、小批量生产的弊端
传统JIT生产方式是从丰田汽车公司规模生产的实践中总结出来的,以纸质看板为手段、以需求为驱动的“拉动”式生产方式,用于多品种、小批量产品的生产,存在诸多弊端。
1)传统看板手段的落后,不利于信息管理。传统看板采用纸质看板,其数据无法直接传递给计算机信息系统,不利于信息的处理,导致计划与预测能力不足。
2)对小批量生产,难以实现传统的拉动方式。由于批量小、工序周期短,末道工序尚未开始生产,首道工序已完成整个批量的生产,因此现场若无同品种的上批次在制品保留,则无法形成“需求拉动”式的生产。
若要用传统看板方式实现小批量的“连续的”拉动生产,就必须在生产现场保留各个品种产品的物料和在制品,这样就造成了大量堆积。故大多数企业的小批量订单式生产,仍主要采用推式生产方式,即生产指令下达到每道工序,但如此又无法实现及时的按需生产。
3)多品种频繁交替生产时,传统看板频繁切换容易出错,并且看板的保管也是个问题。对于有些产品,生产一次后间隔很长时间才会再次生产,看板的保管和使用比较麻烦。
4)缺乏对全局看板信息的掌握,无法提供全面的、实时的生产现场看板流程和各工序看板状态的整体描述,在品种、批次频繁切换的生产环境下容易出现混乱。
2、实现多品种、小批量JIT生产的解决方案
2.1 可视化看板系统的应用场景
可视化看板系统由信息系统、电子看板和条形码扫描输入终端组成。其中的信息系统是融合了精益生产方式的ERP系统,在此基础上新增了可视化看板模块。
2.2 可视化看板系统运行流程
适用于多品种、小批量订单生产的可视化看板系统的运行流程,ERP系统中的MRPⅡ投产顺序计划模块。
以SMT工序的电子看板为例,其运行流程如下。
1)由MRP-Ⅱ生成自制件(PWBA板)的“投产顺序计划”,安排1周的多品种投产顺序和数量。
2)采用可视化看板技术,进行该工序的看板排程,安排工序作业顺序。
3)生成新的“空”生产看板(Production Kanban,PK),通过电子看板下达到工序现场;扫描主件PCB条形码,开始生产,此时看板状态为“在制”。
4)当规定数量的制品生产完成,扫描条形码,则该枚看板的状态变为“满”。
5)当“满”看板枚数达到规定数量时,该看板的生产暂停,直到有新的、补充“空”看板下达才再次起动该看板的生产。与传统看板不同的是,此时系统可以根据看板排程的顺序,接着下达另一订单的“空”看板,起动其生产。
6)当后道工序“取走”物料,此时若该订单的总量尚未完成,则自动发行补充数量的新“空”看板;若已完成,则该生产看板的循环全部“结束”,接下来按照排程下达另一订单的新“空”看板。
7)若后道工序出现异常情况导致对物料的消耗暂停时,看板状态始终为“满”,则不会有该物料的新“空”生产看板下达,生产暂停,从而避免了现场在制品的堆积。
工序间取料看板(Withdrawing Kanban,WK)的主要作用是领用补充物料时指示取货的地点和数量。它通常可以被反复使用,并且取料过程可以不占用工序内时间,因此, 可视化看板系统 中取料看板的形式仍可以采用打印的、带条形码的纸质看板,按照传统方式运行流转。当然也可以采用基于RFID的电子看板。
原文网址:http://www.hzjux.com/xinwenzixun/dianzikanbanxitongzixun/490.html