随着我国人口红利的消失,轮胎行业人工成本逐年上升,人力资源紧张;同时在中国制造2025的时代背景下,中国轮胎产业正向自动化、信息化、智能化、绿色环保方向快速发展。
井源机电是一家专注于移动机器人、自动化物流系统、智能装备系统解决方案的国家高新技术企业,井源机电先后给森麒麟泰国工厂、合肥万力、华谊泰国工厂提供AGV智能物流系统,涵盖半钢、全钢轮胎工厂,使用区域包含炼胶、压延、部件、成型、硫化等工艺。
炼胶车间AGV智能物流
炼胶车间:采用AGV系统实现密炼机生产线胶料的自动搬运、存储、识别管理,以及空托盘的自动码垛、回收。母炼机、终炼机下线生产的胶料自动叠盘,AGV搬运胶料分别送至母炼胶、终炼胶暂存区,AGV具备WMS仓储管理能根据胶料规格型号自动存放管理;MES计划下达生产指令后,AGV将母炼胶暂存区胶料,送至终炼胶上线位置,并将空托盘回收;终炼胶暂存区胶料,送至部件车间压延压出机上线位置;密炼机上下胶片处设计有输送线,实现胶片自动输送、缓存,以及空托盘自动输出。
炼胶车间AGV物流特点:
1) AGV系统自带WMS系统,对多种规格胶片的仓储和出入库管理;
2) AGV自动搬运胶片、自动码垛空托盘,上下线、出入库;
3) 暂存区域采用平面仓储方式,大幅降低仓储成本;
4) 密炼机上下料端采用输送线实现胶片的自动缓存和输送,空托盘自动输出;
部件车间AGV智能物流
部件车间:采用AGV系统实现压延压出生产线胶料、以及空托盘/空台车的自动搬运、存储、识别管理。根据MES计划,AGV将所需规格的终炼胶搬运至对应压延压出线上胶位置,并将空托盘码垛回收入库;AGV将压延压出线部件台车搬运至部件暂存区存放管理,并将空台车搬运至对应压延压出线下线收料位置。
针对半钢和全钢轮胎工厂工艺的差异,我们采用不同的AGV实现部件的搬运,例如胎面部件,半钢工厂采用工字轮台车卷取胎面,由叉车AGV搬运台车出入缓存库存放管理;全钢工厂采用格栅车承接胎面,则采用承载式AGV直接潜入举升承载胎面格栅车,胎面AGV负载≥4吨,可以在水平方向全方位运行,更加灵活,能将胎面格栅密集存放,大大节省占地面积;
部件车间AGV物流特点:
1) AGV系统自带WMS系统,对多种规格胶片的仓储和出入库管理;
2) 压延压出上料端采用输送线实现胶片的自动缓存和输送,空托盘自动输出;
3) AGV自动搬运胶片、自动码垛空托盘,上下线、出入库;
4) 暂存区域采用平面仓储方式,大幅降低仓储成本;
5) AGV自动将满台车送入存储区,并将空台车从存储区送至机台预备位
成型车间AGV智能物流
成型车间:通过AGV系统实现成型机所需部件的智能化配送。根据MES生产计划,需要生产的轮胎规格排班到对应成型机,而成型机需要的各种物料也发送到AGV系统,AGV将暂存区的内衬层、胎面、胎侧、胎圈、胎体、带束等部件,运至成型机上料等待位,并将对应空台车运回暂存区存放。
硫化车间AGV智能物流
硫化车间:AGV主要用于胚胎至硫化机台的自动化配送,以及模具仓储和搬运。
胚胎物流采用AGV承载胚胎车送至硫化机边,一般胚胎车可以承载4个或6个胚胎,提高搬运效率;
模具仓储采用高货架多层形式,AGV自带WMS系统,模具规格、型号、货位都由AGV系统实现智能化管理,当收到模具更换信息,堆垛型AGV自动至对应模具货位叉取模具托盘,送至模具组装区域,并将换下的模具送至对应货位;采用AGV+货架的形式,既实现了模具的仓储管理,又实现了模具出入库的搬运;该堆垛型AGV举升高度可达8米,自动叉取高货位托盘,无需人工干预,安全可靠。
AGV智能物流在轮胎行业运用形式和特点
根据轮胎生产工艺的特点,AGV智能物流在轮胎行业运用,主要以FX叉车型和CX承载型为主;
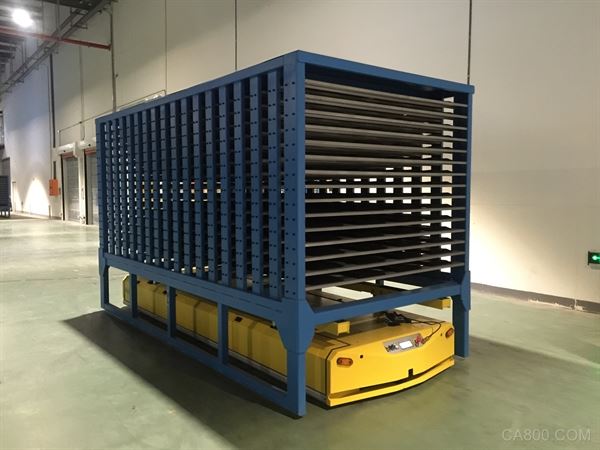
总体而言,AGV智能物流系统在轮胎生产工艺中优势表现如下:
1) MAX调度管理系统,实现JIT(Just In Time)作业,
2) 系统内置WMS系统,数字化仓储管理;
3) 结合MES实现数字化排产,实现严格的先入先出管理;
4) 7×24作业,零安全事故、零出错率、零损失;
5) 降低运营成本:投资回收期3-4年。